Your guide to choosing the right partner for pharmaceutical quality control services
Medicine is the science and practice of maintaining health and preventing, curing disease.Before consuming any type of medicine, they need to be tested and approved for consumption in prepared pharmaceutical laboratories, so that they can be sold and consumed by the population. Keeping patients safe and following the rules set by the government are the most crucial things. Quality control services are like a guide in this complicated process. This guide is made especially for people who make decisions in pharmaceutical companies. It helps you know what to look for when choosing a supplier for your medicines. This way, you can protect your brand and make your process of creating and making drugs even better.
Understanding the pharmaceutical quality control
Quality control (QC) in the pharmaceutical industry is a set of procedures to ensure the identity and purity of a pharmaceutical product. It’s a fundamental aspect of the industry, ensuring the safety and efficacy of drugs and maintaining the integrity of the supply chain. The main objective of quality control in the Pharmaceutical Industry is the drug analysis and testing in their various stages of production, verifying that they are able to proceed to the next stage and release the manufacturing process in accordance with the FDA quality control regulations and specifications required for consumption.The pharmaceutical quality control services include many different parts, each playing an important role:
- Analytical testing: Ensures the purity, potency, and identity of materials and finished products using sophisticated analytical techniques.
- Microbiological testing: Safeguards against microbial contamination, protecting patients from potentially harmful pathogens.
- Environmental monitoring: Monitors air, water, and temperature conditions to guarantee a sterile and controlled production environment.
- Stability testing: Assesses the shelf life and degradation profile of drugs, ensuring efficacy throughout their lifespan.
- Packaging and labelling inspection: Verifies conformity to regulations and ensures accurate information reaches patients.
- Validation and calibration: Guarantees the accuracy and reliability of equipment used in testing and manufacturing processes.
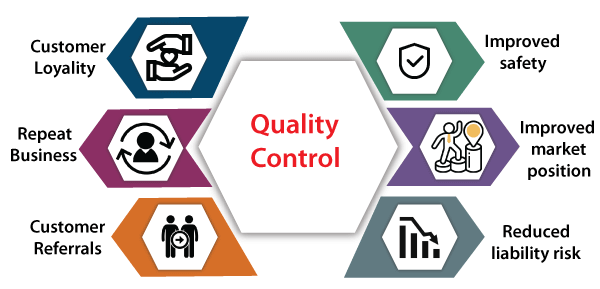
Source: Tutor Aspire
Market trends and key drivers
Pharmaceutical quality control refers to the integration of all procedures undertaken to ensure the identity and purity of particular pharmaceutical products. The rise in awareness for quality control of pharmaceuticals products is helping the global pharmaceutical quality control market to grow at a rapid rate. The increase in the development of comprehensive analytical tests drives market growth. The demand for integrated analytical services spanning all stages of drug discovery, development, and manufacturing also drives the market growth to further height.
Pharmaceutical quality control market which was USD 2,316.5 million in 2022, is expected to reach USD 4,866.24 million by 2030, and is expected to undergo a CAGR of 10.23% during the forecast period.
Source: Data Bridge
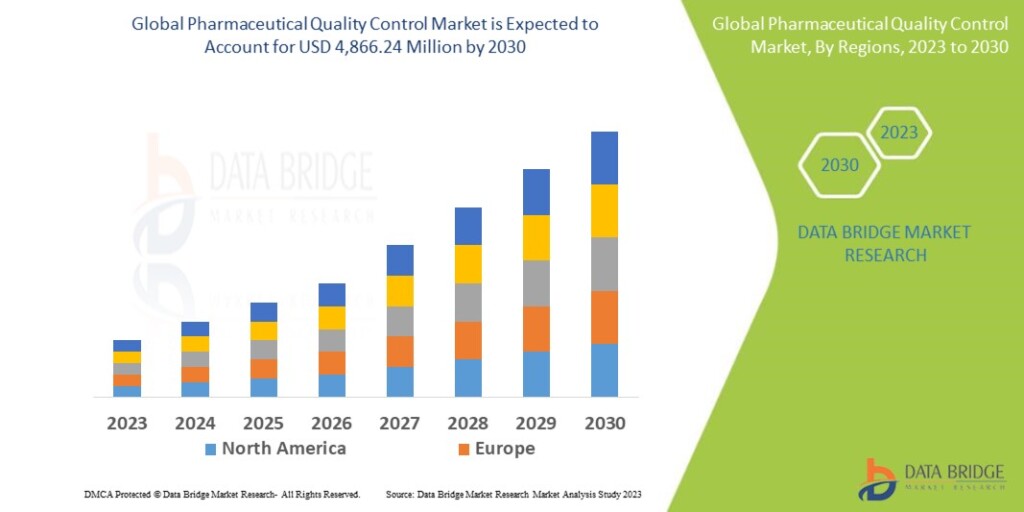
Key trends
pharmaceutical quality control is constantly evolving, driven by technological advancements, changing regulations, and patient safety concerns. Here are some key trends:
Advanced Technology Adoption: Pharmaceutical companies are increasingly incorporating advanced technologies such as artificial intelligence, machine learning, and automation into their quality control processes. This helps in improving efficiency, accuracy, and speed in analysing and ensuring the quality of pharmaceutical products.
Data Integrity and Security: There is a growing emphasis on ensuring the integrity and security of data in pharmaceutical quality control. This involves implementing robust data management systems and cybersecurity measures to protect sensitive information related to drug development and manufacturing.
Regulatory Compliance: Given the highly regulated nature of the pharmaceutical industry, adherence to evolving regulatory standards and compliance requirements is a constant trend. Quality control services need to stay updated with the latest regulations to ensure that pharmaceutical products meet the necessary standards.
Risk-Based Approaches: Pharmaceutical companies are increasingly adopting risk-based approaches to quality control. This involves identifying and prioritising potential risks in the manufacturing process and focusing quality control efforts where they are most needed.
Outsourcing and Collaboration: Some companies are opting for outsourcing certain aspects of their quality control processes to specialized service providers. Collaborative efforts between pharmaceutical companies and quality control service providers are on the rise to leverage expertise and resources more effectively.
Focus on Patient-Centric Quality: There is a growing emphasis on ensuring that quality control measures contribute to the overall safety and efficacy of pharmaceutical products for patients. This patient-centric approach involves considering the end-user experience and outcomes in quality control strategies.
Environmental Monitoring: Environmental monitoring within pharmaceutical manufacturing facilities is gaining importance. This involves assessing and controlling factors like air and water quality to maintain optimal conditions for drug production.
Key drivers
The market for quality control services is growing really fast because of some important reasons.
- Stringent Regulatory Requirements: The pharmaceutical industry is subject to strict regulations and quality standards imposed by regulatory bodies worldwide. Compliance with these regulations drives the demand for robust quality control measures
- Increasing Focus on Patient Safety: Patient safety is a critical concern in the pharmaceutical industry. Quality control ensures that drugs are safe, effective, and free from contaminants, ensuring patient well-being and trust in pharmaceutical products
- Growing Generic Drug Market: The expanding market for generic drugs necessitates stringent quality control to ensure bioequivalence and meet regulatory requirements. Quality control plays a crucial role in maintaining the safety and efficacy of generic drug formulations
- Sustainability in focus: Environmental regulations and consumer awareness are driving demand for eco-friendly quality control practices and waste reduction strategies.
Benefits
The advantages of partnering with good quality control service provider has lots of benefits.
Enhanced compliance
- Gain peace of mind with expert guidance on navigating complex regulations and maintaining impeccable quality standards.
Reduced risk of contamination and errors
- Minimise the risk of defective products reaching the market, protecting your brand reputation and patient safety.
Faster product development and launch
- Streamline processes and accelerate product approvals through streamlined testing and documentation.
Improved operational efficiency
- Leverage advanced technologies and expertise to optimise manufacturing processes and minimise waste.
Access to specialised expertise
- Gain access to cutting-edge analytical equipment and skilled personnel not readily available in-house.
Cost-effectiveness
- Outsource expertise instead of investing in expensive equipment and training, freeing up resources for core activities.
Challenges
- Complex Supply Chains: The pharmaceutical industry relies on global supply chains, making quality control challenging due to factors like transportation, storage, and distribution across various regions. Ensuring consistent quality throughout the supply chain is a significant challenge
- Analytical Method Validation: Validating analytical methods used in quality control is crucial for accurate and reliable results. Developing and validating robust methods for complex drug formulations and diverse matrices can be a challenge for pharmaceutical quality control laboratories
- Finding the right partner: Choosing the right quality control service provider is crucial. Factors like expertise, experience, technology capabilities, cost, and geographical reach need careful consideration to ensure a good fit for your specific needs.
- Cost and resource allocation: Setting up a thorough quality control system can cost a lot. It means spending money on fancy equipment, hiring skilled people, and keeping things running, which adds up over time. Figuring out how to manage these costs alongside other things we need in the company can be a bit tricky.
- Regulatory compliance: In the medicine business, the rules are always changing. We have to follow GMP compliance for pharmaceuticals like cGMP and ICH Q9. Keeping up with these rules is a bit tough for both our team inside the company and the ones we get help from outside.
- Managing communication and collaboration: Effective communication and collaboration between internal teams, external providers, and regulatory agencies are essential for successful quality control implementation. Establishing clear lines of communication and resolving conflicts can be challenging, especially in geographically dispersed or complex setups.
Opportunities
- Increasing Global Pharmaceutical Production: The growing demand for pharmaceutical products, driven by population growth and rising healthcare needs, presents opportunities for the expansion of quality control services to meet the rising production volumes
- Outsourcing of Quality Control Services: Many pharmaceutical companies outsource their quality control activities to specialized service providers. This trend creates opportunities for contract research organisations (CROs) and third-party laboratories offering quality control services
- Technological Advancements: The use of advanced technology in quality control presents opportunities to improve efficiency and accuracy in testing and analysis.
- Global Expansion: As pharmaceutical markets expand globally, there’s a need for quality control services to ensure consistency and compliance across different regions.
- Outsourcing: Companies looking to streamline operations may outsource their quality control needs, creating opportunities for service providers.
- Regulatory Changes: Changes in regulations often lead to new opportunities for services that help companies adapt and stay compliant.
- Data Management: With an increasing emphasis on data integrity, there are opportunities for services that specialise in secure and efficient data management.
- Customised Solutions: Tailoring quality control services to meet specific needs of pharmaceutical companies provides opportunities for niche service providers.
- Collaboration and Partnerships: Forming partnerships with pharmaceutical companies for comprehensive quality control solutions can be a strategic opportunity.
- Focus on Patient-Centric Quality: Services that prioritise patient safety and satisfaction align with the growing trend of patient-centric healthcare.
- Environmental Monitoring: As environmental considerations become more important, services focusing on monitoring and maintaining sustainable practices in pharmaceutical production have opportunities
Key players
Some of the major players operating in the pharmaceutical quality control market are
- Merck KGaA (Germany)
- BioMérieux SA (France)
- Charles River Laboratories International, Inc. (U.S.)
- Sartorius AG (Germany)
- WuXi AppTec (China)
- Thermo Fisher Scientific, Inc. (U.S.)
- SGS S.A. (Switzerland)
- Eurofins Scientific (Luxembourg)
- Toxikon Corporation (U.S.)
- McKinsey & Company (U.S.)
- Esco Micro Pte. Ltd (Singapore)
- Lucideon Limited (U.K.)
- PerkinElmer Inc. (U.S.)
- SOLVIAS AG (Switzerland)
- Shimadzu Scientific Instruments (Japan)
- METTLER TOLEDO (Switzerland)
- REMI GROUP (India)
- BRAM-COR SPA (Italy)
- Panomex Inc. (India)
- Waters Corporation (U.S.)
- Danaher (U.S.)
How to find the best quality control services partner
Finding the best quality control services partner is crucial for ensuring the safety and reliability of pharmaceutical products. Here are steps to help you find the right partner:
Define Your Needs
- Clearly outline your quality control requirements and the specific services you need.
Research and Shortlist
- Research potential partners. Look for companies with a good reputation, relevant experience, and positive client reviews.
- Shortlist a few candidates based on their expertise and capabilities.
Credentials and Compliance
- Check the credentials and certifications of potential partners. Ensure they comply with industry standards and regulations.
Experience in Pharmaceuticals
- Prioritise partners with experience in the pharmaceutical industry. Familiarity with regulatory requirements is essential.
Technology and Methods
- Evaluate the technology and methods the partner uses for quality control. Ensure they employ up-to-date and efficient processes.
Track Record
- Look into the partner’s track record. Assess their performance history and success in delivering quality control services.
Communication and Transparency
- Assess communication practices. A good partner should be transparent, responsive, and willing to discuss their processes.
Flexibility and Scalability
- Consider the partner’s flexibility and scalability. Ensure they can adapt to your company’s changing needs and growth.
Site Visits and Audits
- Arrange site visits and audits to assess the partner’s facilities and quality control processes firsthand.
Cost and Value
- Compare costs among potential partners but also consider the value they provide. Sometimes a higher upfront cost can lead to better long-term outcomes.
References
- Ask for references from current or previous clients. This can provide insights into the partner’s reliability and performance.
Legal and Contractual Aspects
- Review legal aspects and contracts carefully. Ensure there is a clear understanding of responsibilities, timelines, and any potential legal implications.
Collaboration and Cultural Fit
- Assess the potential for collaboration and the cultural fit between your company and the partner. A good working relationship is vital.
Continuous Improvement
- Inquire about the partner’s commitment to continuous improvement. Quality control processes should evolve with industry advancements.
Trial Period
- Consider starting with a small-scale project or trial period to assess the partner’s capabilities before committing to a long-term partnership.